Perkusista odwiedza fabrykę DW
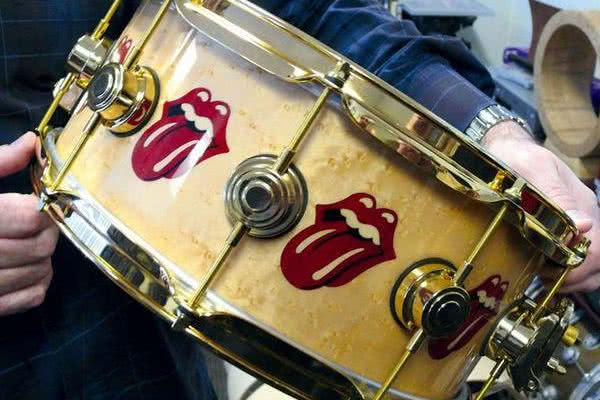
Zestaw bębnów DW to dla wielu perkusistów wielkie marzenie. Jak wygląda fabryka legendarnego już producenta? Czy rzeczywiście wszystko jest robione tam ręcznie? Jak wygląda selekcja i dobór materiału? Zobaczcie naszą galerię i relację.
W numerze 5/2010 odwiedziliśmy szwajcarską fabrykę talerzy Paiste. Przyszła więc kolej na odwiedziny firmy produkującej bębny. Wybraliśmy dla was fabrykę DW, która ma siedzibę w Kalifornii w Oxnard. Firma była świeżo po targach NAMM i od razu zastrzegła, że w paru miejscach mogą być nie do końca przygotowani do naszej wizyty jak należy. Finalnie wszystko przebiegło lepiej niż dobrze! Fabryka umiejscowiona jest w dwóch olbrzymich budynkach, które robią spore wrażenie i natychmiast wymazują wizję skromnej manufaktury z kilkoma zakręconymi stolarzami i tlenioną panią księgową. Okolice fabryki to krajobraz bardzo podobny do podwarszawskich terenów, gdzie pola warzywno-owocowe przeplatają się z magazynami i dużymi fabrykami. W takim właśnie kompleksie budynków i sąsiedztwie pół truskawkowych zaopatrujących całe megalopolis Los Angeles znajduje się siedziba DW.
W progu wita nas uśmiechnięty John Good. Ubrany w koszulę i dżinsy kłóci się nieco z wizerunkiem, do jakiego przyzwyczaił nas podczas targów, gdzie zawsze elegancko, w garniturze i pod krawatem z niezwykłą klasą, ale i typowo amerykańskim luzem rozprawia niezwykle ciekawie o filozofii DW. Tu, na swoich śmieciach, w dniu roboczym, przywitał cały nasz polski "gang" (plus dwóch czeskich reprezentantów) z wielką serdecznością, zapraszając ochoczo do środka. Przechadzając się po salach i pokojach fabryki przedstawiał nas jako swoich "polskich przyjaciół", co trzeba przyznać, było także przyjemne i budujące. Głównie jest to zasługa dystrybutora DW na Polskę, który w taki sposób reprezentuje nasz kraj na arenie międzynarodowej. Przejdźmy się więc razem z Johnem Good po fabryce.
Tu leżą wszelkiego rodzaju arkusze drewna, które będą składać się na korpus bębna. John ma ich olbrzymią kolekcję z całego świata. Jednym z jego zadań jest poszukiwanie odpowiedniego budulca. Robi to niemal na każdym kontynencie, za wyjątkiem Antarktydy, chociaż? kto go tam wie.
Niektóre z gatunków mają wręcz niesamowitą strukturę, przez co można się zastanowić, czy to aby na pewno drewno i czy na pewno jest to dzieło natury. Przypominamy, że każde ścięte drzewo przez firmę to obowiązek posadzenia dwóch kolejnych.
Pod tabliczkami informacyjno-ostrzegawczymi prasa zgniata ze sobą kolejne warstwy drewnianych arkuszy. W wysokiej temperaturze przez trzy minuty arkusze łączą się ze sobą.
Zgniecione i połączone ze sobą warstwy są teraz przycinane do odpowiedniego rozmiaru po to, by za chwilę komponować z nich odpowiednie rozmiary i konfiguracje korpusów. Jak widzicie - "rozmiar ma znaczenie".
Pracownik zebrał właśnie kilka zgniecionych ze sobą arkuszy i skonfigurował z nich odpowiedni korpus do centralki. Każdą stronę posmarował klejem i złożył "na zakładkę". Z prawej strony widać wałki magla, które precyzyjnie pokrywają warstwy klejem.
Teraz skonfigurowane kadło jest wsadzane do maszyny, która połączy wszystkie warstwy w jedną solidną całość.
W tym miejscu rozciągane są korpusy, by wkleić odpowiednio zewnętrzne ringi.
Następuje teraz żmudna obróbka powstałych korpusów, szlifowanie i nadawanie precyzyjnej formy danego korpusu. Jak widzicie, wymagany jest do tego odpowiedni sprzęt zabezpieczający, żeby nie nałykać się pyłu. Kadłuby są wygładzane, polerowane i przygotowywane do kolejnego etapu, jakim będzie naniesienie odpowiedniej warstwy lakieru.
W tym miejscu sprawdzana jest równość korpusu. Czy aby postawiony pionowo nie zacznie się kołysać? Jest to po etapie szlifowania kolejny punkt weryfikacji jakości bębna.
Za tymi drzwiami, jak sama nazwa wskazuje, dokonywane jest wykończenie Satin. Ze względu na wykorzystywane lakiery odbywa się to za zamkniętymi drzwiami.
A ten mały przyjaciel nie jest bynajmniej opuszczoną maszynką do centralki. Z racji tego, że ze względów bezpieczeństwa drzwi otwiera pracownik z wewnątrz lakierni, a maszyny mają swoją głośność, potrzebna jest dobra? kołatka.
Tak wyglądają suszące się po lakierowaniu tradycyjne korpusy DW. Ze względu na wymogi temperatury i wilgotności, a także - rzecz jasna - ze względów bezpieczeństwa odbywa się to w zamkniętych, odizolowanych pomieszczeniach.
Jak widać, pracownicy lakierni także w pełni korzystają ze sprzętu zabezpieczającego, ponieważ opary lakieru nieźle mogłyby przeczesać komórki naszego mózgu i wywlec płuca na lewą stronę. Wszyscy fani zestawu "Mały chemik" powinni być wniebowzięci.
Nie każdy bęben to instrument lakierowany. W niektórych zestawach mamy zastosowaną interesującą okleinę. Przy pomocy takiego właśnie magla jest ona nakładana.
Tak wyglądają idealnie wykonane korpusy DW, świeżo po wysuszeniu, prawdziwe dzieła sztuki.
Louie Garcia to istny artysta. Ten uzdolniony graficznie pracownik firmy zajmuje się indywidualnymi zestawami, takimi chociażby jak bębny Neila Pearta, które spowodowały tak wielki zawrót głowy na targach NAMM 2011 (pisaliśmy o tym w "Perkusiście" 2/11). Mozolny proces nakładania pojedynczo (!) każdej grafiki można zaobserwować chociażby po robionym przez Louiego werblu właśnie Neila Pearta, widocznym na zdjęciu.
Nadszedł czas, by nasze korpusy uzbroić w odpowiedni hardware. Dlatego też trzeba z niezwykłą precyzją nawiercić otwory w kadłubie.
Nowa maszyna robiąca otwory, w pełni skomputeryzowana, wysyła maila, że wykonała właśnie określone zadanie. Nie ma możliwości, by coś zostało nierówno lub krzywo nawiercone.
Ten znaczek jest znany chyba każdemu fanowi rocka, ale pewnie nie tylko. Werbel dla Stonesów jedynie pozornie posiada naniesioną zwykłą grafikę słynnego wzoru. Tak naprawdę każdy oddzielny kolorystycznie element to inny kawałek drewna! Precyzja wykonania godna największych mistrzów.
Ten znaczek mówi chyba wszystko za siebie, wchodzimy do strefy Johna Good!
W tym miejscu John Good dokonuje ostatecznej selekcji poszczególnych korpusów bębnów, komponując z nich określony zestaw. Sprawdza dokładnie parametry każdego korpusu, w tym także brzmienie poszczególnych kadłubów, układ słojów oraz ich kolor. Jego siedziba znajduje się tuż pod dachem fabryki i rozpościera się z niej widok na większość działów produkcyjnych. Zebrany zestaw idzie do dalszej obróbki, o której wspominaliśmy wcześniej. Konfiguracja określonych zestawów zależy więc od Johna.
Także w tym miejscu dochodzi do kolejnej kontroli jakości, gdzie sprawdzane jest brzmienie poszczególnych kadłubów, ale także po raz kolejny równość krawędzi. Jak wiadomo, każdy bęben DW ma oznaczony dźwięk, w jakim wybrzmiewa. Do tego celu służy widoczny mikrofon, gdzie ustalany jest dźwięk kolejnego bębna, czekającego już tylko na swoje stalowe "ubranie".
Wreszcie nasze bębny ubierane są w odpowiedni hardware. Tu już nie ma maszyn, które byłyby w stanie zastąpić rękę człowieka. Panie za pomocą wkrętarek (te żółte sprężynki) zakładają wszystkie lugi i mocowania. Zwróćcie uwagę, że bęben, który jest właśnie obrabiany, zabezpieczany jest przed zniszczeniem krawędzi podczas montażu.
Pełna garderoba obręczy.
Aż w końcu dochodzimy do punktu kulminacyjnego naszego procesu produkcji słynnych DW. W tym miejscu składany jest cały zestaw beczek. Każdy dostaje swój numer identyfikacyjny, każdy zestaw ma również robione zdjęcie. Potem już tylko ląduje w pudełkach i czeka na swojego szczęśliwego posiadacza.
Oprócz bębnów DW drums mamy także hardware w postaci stopek i statywów. Firma ma więc u siebie dział produkujący komponenty do poszczególnych konstrukcji oraz dział montażowy. Dodatkowo olbrzymi magazyn, w którym cały czas jest wielki ruch. Ale to nie wszystko! Jak wiadomo DW to już instytucja, która swoim zasięgiem sięga zdecydowanie dalej aniżeli konstruowanie bębnów najwyższej klasy. To cała filozofia i przede wszystkim bardzo poważny biznes. Dlatego też fabryka wykracza zdecydowanie poza ramy produkcyjne. Zróbmy więc rundkę po dalszej części fabryki, by odkryć, co tam jeszcze kryje się w jej zakamarkach. Zacznijmy jednak od szybkiej przebieżki przez dział z hardware.
Te mało atrakcyjne maszyny zajmują się wyjątkowo mało atrakcyjnym wyrobem części składowych poszczególnego hardware?u. Skupmy się bardziej, co się dzieje, gdy wszystkie drobiazgi są już przygotowane do złożenia.
A tu nie lada ciekawostka. W małej skrzynce wytłumionej gąbką znajduje się stopka perkusyjna z kolejnej partii montażowej, która jest testowana za pomocą urządzenia, które ma symulować grę nogą. Chodzi tu oczywiście jedynie o wytrzymałość sprzętu. Stopa wykonuje kilka tysięcy uderzeń, miarowo postukując.
No i tu już się zaczynają bardzo ciekawe widoki. O ile wcześniej mieliśmy oczopląs, wywołany szarańczą beczek DW, tak tutaj rozpoczynamy od hi-hatów.
Na tych stołach jest składany do kupy i segregowany cały hardware.
Prawdopodobnie wielu z was zrobi się słabo na taki widok stopek DW. Z naszej strony dodamy, że wygląda to jeszcze bardziej atrakcyjnie, gdy ogląda się to na żywo.
Przechodzimy już do pozaprodukcyjnej części fabryki, a mianowicie do studia nagrań, gdzie nagrywane są materiały między innymi dla strony drumchannel.com. Olbrzymie studio nagrań z dwupoziomową reżyserką. Wspaniała akustyka przestronnej sali, idealnie pasującej do nagrań bębnów. Cóż można chcieć więcej? Tylko pozazdrościć, że fabryka produkująca bębny ma studio nagrań, które w naszym kraju zaliczałoby się do czołówki.
Chyba każdy wie, czyje to bębny? Obecność Terry?ego Bozzio zauważalna jest właściwie na każdym kroku w fabryce. Tymczasem w jednym z pokojów ma on swoją własną ćwiczeniówkę. Nie widać tego na zdjęciu ze względu na światło, ale najwyższy punkt ramy, nad gongiem, jest wbity w sufit, ponieważ bębny są za wielkie?
Tu już znajdujemy się w "John Good Gallery". Obszerna sala z kilkunastoma zestawami perkusyjnymi różnej maści. Specjalny zbiór bębnów wykonanych przez Johna nieraz z naprawdę kosmicznych gatunków drewna. John, komentując niektóre z bębnów swojej galerii, mówił "Och, drewna z tego zestawu mam jeszcze może na 3-4 zestawy więcej". Na zdjęciu od lewej stoją: John Good, Michał Dąbrówka, Petr Kudibal z czeskiej dystrybucji DW oraz Scott Garrison, odpowiedzialny za kontakty z artystami w firmie.
Fabryka robi wrażenie i nie da się na kilku stronach, w kilku zdjęciach opisać tego, jak potężny jest to kompleks i jak dokładnie wykonywane są bębny. Zapewne niektórzy z Was słyszeli lub może nawet sami mieli do czynienia z bębnami DW, które miały jakiś drobny uraz. Po naszej wizycie i dość wścibskiej penetracji sal i maszyn zdecydowanie i bez odrobiny zawahania twierdzimy, że jeżeli cokolwiek złego dzieje się z bębnami DW to jest to kwestia transportu (temperatura, ciśnienie, wilgotność) i ewentualnie załadunku/rozładunku. W etapie produkcyjnym np. Collectorsów, które chociażby prezentowaliśmy w wielkim teście w numerze 1/11, nie ma możliwości na przepuszczenie jakiegokolwiek błędu czy wady. Bębny sprawdzane są kilkakrotnie na różnych etapach składania, oprócz tego niektóre elementy wykonywane są przez maszyny (jak chociażby rozkład dziur na hardware bębnów), ponieważ robią to precyzyjniej i dokładniej. Finałowa kontrola jakości, strojenie oraz fotografowanie sprzętu dodatkowo zmusza do idealnego wykończenia beczek. John Good ma nad wszystkim pieczę i po ilości arkuszy drewna, jakie pokazał nam na wstępie, oczekiwać można kolejnych interesujących rozwiązań. To ewidentny pasjonat i fachowiec z najwyższej półki. Zaraz po naszym tour John zaprosił nas wszystkich na obiad, na który udaliśmy się jego czarnym ponad czterystukonnym Infiniti. Tam już wesołe rozmowy i luźne historie, a także zaproszenie do naszych lasów na drzewne łowy. Wyobraźcie sobie - mieć bębny DW wykonane z polskiego drzewa! John opowiedział nam kilka ciekawych muzycznych historii, po czym w promiennych nastrojach udaliśmy się w swoje strony. Klasa moi drodzy, klasa, że aż przyjemnie wspominać?
Wizyta w fabryce DW nie odbyłaby się bez pomocy dystrybutora sprzętu DW na Polskę, firmy PMI - DW Drums Polska. Wielkie podziękowania dla wspaniałych kamratów naszej wycieczki (ach ten palec!), naszych czeskich przyjaciół, a przede wszystkim Dąbrówera oraz dla Richarda Lenarczyka - również za bezpieczny transport.