Z wizytą w fabryce Remo
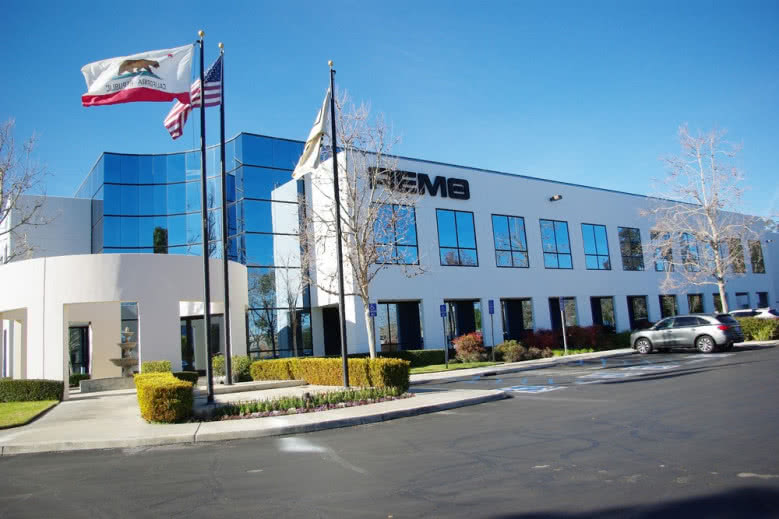
Jest to jeden z najbardziej znanych producentów sprzętu w świecie perkusji. Marka, która łączy nie tylko stylistyki muzyczne poprzez różnorodność swoich artystów, ale również łączy ze sobą chyba wszystkich producentów bębnów na świecie.
Nieważne, czy grasz metal, jazz, hip-hop, nieważne, czy stać cię na wielkie DW, czy tylko na przeciętnego Mapexa, nieważne, czy zaczynasz grać, czy też jesteś zawodowcem. Na Remo gra większość bębniarzy, a znają firmę wszyscy.
Firma zaprosiła nas do siebie już w zeszłym roku. Mieliśmy umówioną konkretną wizytę zaraz po targach NAMM. Możliwość odwiedzenia legendarnej fabryki wydawała się bardzo ekscytująca. Odwiedziliśmy już wielu producentów talerzy i bębnów. Proces tworzenia instrumentów w tych miejscach na ogół jest bardzo podobny, a niekiedy wręcz identyczny. Różnice dotyczą naprawdę detali (które często w dużej mierze wpływają na jakość produktów). Odwiedziny fabryki naciągów to inna sprawa, inna technologia, kompletnie inny proces produkcji. To po pierwsze.
Po drugie, w świecie perkusji mamy olbrzymią ilość producentów bębnów, talerzy, pałek, ale raptem kilku produkuje naciągi. Remo jest wiodącym ilościowo i technologicznie niedoścignionym liderem. Zaraz po nim plasuje się Evans, a dalej Aquarian i gdzieś na szarym końcu Attack, o kilku malutkich producentach lub też działach produkcji innych firm nie wspominając. A przecież membrana to rzecz, która zawsze będzie potrzebna, która w odróżnieniu od bębnów zużywa się szybko i często. Odpowiedź, dlaczego tak się dzieje, znajduje się właśnie w fabryce w Valencii, ale nie tej słynnej hiszpańskiej, a tej mniejszej, zupełnie bezpłciowej kalifornijskiej.
REMO
Historia marki Remo jest bardzo prostą historią, chociaż niepozbawioną dramatycznych momentów. Prawdopodobnie w momencie, gdy trzymacie niniejszy magazyn w rękach, firma uruchomiła nową stronę (remo.com), która ma ogromne zasoby związane z produktami, ale też właśnie z historią firmy, czyli po prostu z historią bębnienia. Postaramy skupić się tu na najprostszym opisie tego, z czym mamy do czynienia.
Fabryka Remo sięga swoimi korzeniami połowy lat 50 ubiegłego stulecia. Zaraz po zakończeniu drugiej wojny światowej młody perkusista Remo D. Belli zaczął się zastanawiać, dlaczego, do diaska, naciągi w bębnach muszą tak wariować? Chodziło tu głównie o reakcję na zmianę wilgotności powietrza. Skóry były kapryśne i oprócz zmiany stroju, po prostu "zdychały". Okres wojenny to oprócz koszmaru także okres, gdzie powstają szybko nowe rozwiązania techniczne. Pewna uznana amerykańska firma o nazwie DuPont współpracowała z armią i dostarczała jej różne materiały m.in. folię do izolacji w samolotach. Po wojnie temat został rozwinięty, a w połowie lat 50 dzięki obróbce poli(tereftalanu etylenu) (C10H8O4)n powstał dobrze znany Mylar.
Remo Belli przyjrzał się dokładnie folii i doszedł do wniosku, że z racji jej właściwości można spróbować stworzyć z tego naciąg perkusyjny. Tak to się wszystko zaczęło. Remo wiedział, że ciężko będzie przekonać perkusistów do odejścia od tradycyjnych skórzanych naciągów, jednak nieporównywalnie lepsze właściwości sztucznego tworzywa wzięły górę. Najpierw celował w klasyczne białe, przypominające skórę, membrany. Dopiero później zaprezentował przezroczyste, aż w końcu dotarliśmy do momentu, gdzie z naciągiem możemy zrobić praktycznie wszystko, co chcemy.
Mimo początkowego sceptycyzmu, jakość nowych naciągów wzięła górę i cały świat perkusji, łącznie z instrumentami perkusyjnymi i perkusją klasyczną zaczął korzystać z Mylarowych "skór". Proces technologiczny okazał się na tyle skomplikowany, że konkurencja nie wyrastała jak grzyby po deszczu, a firma w pewnym momencie miała monopol na membrany perkusyjne. Fabryka Remo powoli się rozwijała i ostatecznie od 30 lat znajduje się w kalifornijskiej Valencii. Oprócz tego Remo ma swoją produkcję w Chinach.
Remo przyczyniło się znacznie do rozwoju mocnej muzyki.
Remo to nie tylko membrany. Firma znana jest ze świetnych instrumentów perkusyjnych oraz akcesoriów. Swego czasu firma próbowała również swoich sił w produkcji bębnów, osiągając nawet pewne sukcesy, jednak konkurencja była tak duża, że rzucenie sił w tę część rynku nie miało większego sensu, tym bardziej, że to właśnie producenci bębnów byli klientami i użytkownikami naciągów. Obecnie mamy całą gamę naciągów w olbrzymiej ilości wykończeń.
Remo jako jedyne produkuje naciąg 23", który wykorzystywany jest w centralkach DW. Cała gama ciekawych instrumentów perkusyjnych, głównie z kategorii uderzanych i posiadających naciąg (czyli conga, djembe, frame itd.), ale też nie stroni od cajonów i dzwonków. W katalogu są też słynne rototomy. Pamiętać też trzeba o całej masie dodatkowych produktów i akcji, w jakie zaangażowana jest firma. Jest to typ wizjonerski, bardzo podobny do tego, co mamy w przypadku firmy Vic Firth. Wykraczanie poza produkcję, tworzenie społeczności i wzajemnych więzi między artystami, firmami i fanami, wspomaganie i propagowanie gry na instrumentach perkusyjnych na całym świecie.
Odwiedzenie fabryki wydawało się zatem nie tylko wielką przyjemnością, ale też swoistym zaszczytem.
FABRYKA
Główna siedziba Remo znajduje się w Valencii, kilkadziesiąt kilometrów na północ od Los Angeles, prosty dojazd do zupełnie nijakiej mieściny, ot miejscowość, jakich wiele w tej części USA, kompletnie nieatrakcyjne miejsce z którego wieje nudą, coś jak nasz Wołomin. To właśnie tu pod numerem 28101 znajduje się wielki biały budynek - siedziba i główna linia produkcyjna. Pierwszą rzeczą, która rzuca się w oczy jest cała masa nagród i pamiątek porozwieszana po fabryce. Firma dostała ich bez liku i w każdym miejscu widać albo jakieś podziękowania, albo jakąś nagrodę w jakimś plebiscycie lub konkursie. To Ringo Starr, to Neil Peart, to jakaś organizacja, to jakaś rządowa inicjatywa. Nie spotkałem się jeszcze z takim natłokiem wyróżnień w żadnej fabryce, nawet tak ekskluzywnej jak DW czy długowiecznej jak Zildjian!
Oprócz tego… boksy. Pierwsze pomieszczenie po przejściu z recepcji to biura, które wyglądają przerażająco monotonnie. Tylko wspominane nagrody wiszące na ścianach przypominają, że mamy do czynienia z firmą perkusyjną. Po całej dawce kurtuazyjnych czynności przechodzimy do najważniejszego - wizyty na linii produkcyjnej, naszym przewodnikiem jest sam dyrektor produkcji - Herbie May. Przed wejściem na hale uprzedza, że może być dość głośno. Trochę to dziwne, przecież mamy do czynienia z kawałkami folii, po chwili wszystko było już jasne.
Otwieramy drzwi i przed naszymi oczami ukazuje się olbrzymia hala, panuje spory łoskot pracujących maszyn. Mijamy półki z obręczami, są jeszcze w pierwszym stadium (fot. 1),
dopiero później zostaną pocięte na odpowiednie kawałki (fot. 2)
i zostanie uformowana z tego klasyczna obręcz, połączona w gładki sposób, by moment łączenia obręczy był równy (fot. 3),
zaraz po tym obręcze już w całości przechodzą przez kolejny piec (fot. 4)
po którym obręcz wygląda już tak jak powinna. Mijamy szpule z Mylarem czyli materiałem z którego zostaną zrobione naciągi, wyglądają zupełnie niepozornie. Nałożone na wał są gotowe do cięcia na odpowiednie kawałki (fot. 5).
Wielka prasa wbija formę w materiał dzięki czemu mamy idealnie równe kawałki naciągów (fot. 6),
w tym miejscu wybijane są również inne kształty jak np. obręcze. Przechodzimy do etapu, gdzie wokół całego naciągu robione są dziurki (fot. 7),
dzięki temu membrana lepiej i mocniej nam się zahaczy po zalaniu jej w obręczy. Naciąg musi zostać teraz odpowiednio zakrzywiony (fot. 8),
żeby wszedł pod odpowiednim kątem do obręczy. Komplety naciągów leżą luzem w obręczach (fot. 9),
czekają teraz na zalanie (fot. 10)
dzięki temu mamy ostatecznie gotowy najprostszy naciąg, na który nie pozostaje już nic, jak tylko nanieść (fot. 11) odpowiednie napisy informacyjne (logo, model, rozmiar), ale ten etap nie zawsze pojawia się w tym miejscu i najczęściej dzieje się to już po zmagazynowaniu membran.
Firma robi też specjalne naciągi na zamówienie, głównym problemem są tu zazwyczaj rozmiary zamówień (fot. 12).
Remo robi też oczywiście naciągi do bębnów marszowych, których proces tworzenia (fot. 13) odrobinę różni się od tworzenia naciągów zestawowych.
Nie są klejone tylko w pełni zawijane w obręczy wokół stalowych rdzeni. Pracownica sprawdza (14 A) poszczególne egzemplarze z serii czy wszystko jest w porządku.
Trening czyni mistrza, niektóre skazy ciężko dostrzec i w naszych rękach naciąg by przeszedł jako w pełni sprawny, tymczasem nawet drobne skazy kierują produkt do kosza (14 B).
Jak widać, wcześniej naciągi nie mają swoich logotypów. Leżą w magazynie (fot. 15) i czekają na konkretne zamówienie,
bo może się okazać, że dana partia ma iść do DW, Gretscha, Yamahy, Pearla i wtedy trzeba nanieść specjalne logotypy, inne niż fabryczne (fot. 16).
Ostatecznie naciągi są pakowane w pudełka (fot. 17), co pokazywaliśmy na filmie na naszym profilu Facebook i Instagram.
Teraz zostaną wysłane do Europy, USA, Australii, Ameryki Południowej, do najdalszych zakątków, wszędzie tam gdzie są perkusiści. Nie ma tu żadnych półek z tzw. drugim sortem! Naciąg jest albo dobry, albo zły i idzie do kosza. Przychodzi zlecenie np. 10000 membran dla firmy Gewa. Naciągi są szykowane i wysyłane do Niemiec. Stamtąd poprzez Gewa Polska partie idą do polskich sklepów, które złożyły zamówienie. Nikt nie siedzi po drodze i nie segreguje lepsze-gorsze! Tak w skrócie wygląda proces produkcji membran do zestawów perkusyjnych. Jest to proces złożony, gdzie maszyny działają razem z ludźmi. Ważna jest dokładność i precyzja pracownika. Maszyny są specjalnie wykonane dla Remo i to co pokazaliśmy powyżej, to tylko telegraficzny skrót całego procesu produkcji, gdzie nie widać, jak obsługujące poszczególne etapy maszyny są skomplikowane.
Remo w swojej fabryce zajmuje się także produkcją instrumentów perkusyjnych i specjalnych naciągów (fot. 18) do wszystkich możliwych instrumentów, łącznie z naciągami siateczkowymi do cichego grania lub instrumentów elektronicznych.
Zakres jest naprawdę olbrzymi i czasami wręcz niesamowity (fot. 19).
Fabryka ma jeszcze rozbudowany dział graficzny, ale bardzo ciekawym i ważnym działem jest laboratorium czyli dział badań. W tym miejscu oprócz prób z nowymi materiałami sprawdzana jest chociażby wytrzymałość membran poprzez specjalną prasę (fot 20).
Na koniec temat, który ostatnio był bardzo często poruszany w różnych miejscach - powlekanie. Firma Remo zawsze słynęła z jakości swoich produktów w tym z jakości powłoki jaka jest nakładana na gładki Mylar (fot. 21).
Dokładny proces nakładania stanowi tajemnicę firmy, ale sposób pracy maszyny, którą mieliśmy okazję oglądać, jest niesamowity. Nie jest łatwo nałożyć warstwę powłoki idealnie równo na całej membranie, tak jak to robi Remo. Żadna firma nie ma takiej precyzji działania, ale jednak wkradł się ostatnio lekki błąd. Sęk w tym, że jak ów błąd zostanie zauważony po godzinie, to w tym czasie zostanie wyprodukowana cała masa naciągów. Dodatkowo, błąd nie sprawiał wrażenia poważnego i na etapie kontroli jakości w fabryce wydawało się wszystko być ok, nie było. Bob Yerby, szef sprzedaży i marketingu powiedział nam: "Nasz system i rodzaj powłoki się nie zmienił, ale zainstalowaliśmy dodatkową kontrolę produktów dzięki czemu system jest zoptymalizowany, cyfrowa kontrola zapewnia spójność i ciągłość."
Tak naprawdę było to pierwsze pytanie jakie zadaliśmy po przyjeździe do fabryki, nikt nie uchylał się od odpowiedzi, bo okazało się, że problem, nad którym głowi się tylu polskich perkusistów nie jest (zapewne ku zamartwieniu niektórych) żadnym zamachem stanu, przewiertem czy też celowym uderzaniem w polski rynek.
Serdeczne podziękowania dla Gary’ego Manna, Boba Yerby i Herbie Maya za wizytę w fabryce oraz dla Sue Kincade za pomoc z materiałami archiwalnymi.
Artykuł ukazał się w numerze marzec 2016