Powstanie Phoenixa. Ekskluzywna linia Yamahy PHX z Japonii
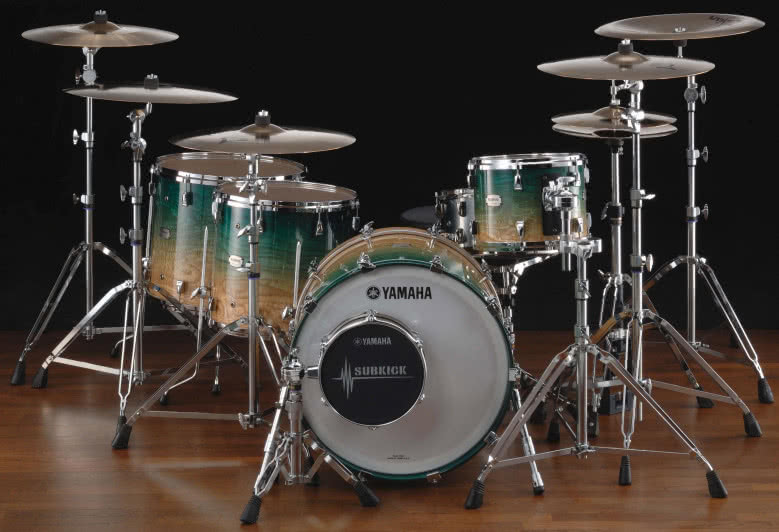
Hamamatsu to miasto położone na południowy zachód od Tokio o trzy i pół godziny jazdy (lub nieco ponad dwie szybkie godziny w futurystycznym pociągu Bullet Train). Właśnie tam Yamaha produkuje na zamówienie wysokiej jakości hybrydową serię PHX.
Jest to znacznie mniejsza placówka niż Xiaoshan, z małą liczbą pracowników, ale to właśnie w tym miejscu narodziły się standardy czystości, dbałość o szczegóły i jakość wykonania, które stosowane są w Xiaoshan. Wiele umiejętności, procesów i wiedzy specjalistycznej opracowanych w Hamamatsu zostało zastosowanych w chińskiej fabryce.
Technicy Yamahy, których można spotkać przy liniach produkcyjnych, mają na swoim koncie wieloletnie doświadczenie i dobrze orientują się we wszystkich aspektach budowy i wykończeń bębnów. Wielu z nich jest perkusistami, a niektórzy należą do lokalnego Yamaha Big Band. Jeżeli zaszłaby taka potrzeba – jeden pracownik byłby w stanie skompletować cały bęben, od początku do końca. Sześć miesięcy zajmuje szkolenie technika w malowaniu bębnów, aby efekt był zgodny z oczekiwanym standardem. Jest to zrozumiałe, gdy przesuwasz palcami po szklistych korpusach i dowiadujesz się, że niektóre wykończenia wymagają do dwudziestokrotnej obróbki. W zależności od rozmiaru i specyfiki bębna może to zająć nawet do stukrotnej obróbki! W tej fabryce robi się od 5 do 10 korpusów dziennie, co jest uzależnione od rozmiarów i złożoności każdego z nich. Na zestaw z Japonii trzeba czekać 6 miesięcy (a na zestaw na zamówienie z Xiaoshan – 4 miesiące). To dość uczciwy czas oczekiwania, gdy chcemy zasiąść za swoją nową dumą i radością. Warto, ponieważ otrzymujemy oszałamiająco dopracowany instrument.
KROK 1 – CIĘCIE I KLEJENIE
Yamaha tnie warstwy z łączeniem diagonalnym. Typowy przy produkcji bębnów proces cięcia i składania, wymaga oczywiście sprawnej ręki fachowca. Później warstwy są gotowe do sklejenia. Klej miesza się ręcznie, niewielką ilość wylewa się na arkusz i rozprowadza równomiernie za pomocą wałka.
KROK 2 – WYPEŁNIANIE FORMY
Po sklejeniu, arkusze z jatoby, kapuru i klonu są wkładane w rozgrzaną formę i lekko wbijane do środka, aż znajdą się na swoim miejscu, a krawędzie ścięcia ciasno przylegają do siebie. Worek Air Seal jest wkładany do środka i nadmuchiwany, co sprawia, że około pięciu kilogramów nacisku działa na całą powierzchnię korpusu. Korpus pozostawia się do „gotowania” w temperaturze 100 °C na godzinę przed ochłodzeniem w temperaturze pokojowej. Można zauważyć wilgoć ulatniającą się z korpusu już kilka minut po podgrzaniu formy. W ciągu 24 godzin klej staje się twardy jak skała.
KROK 3 – PIASKOWANIE I CIĘCIE
Następnie korpusy zostają poddane procesowi piaskowania przy pomocy specjalnie skonstruowanych maszyn. Korpusy są piaskowane wewnątrz i na zewnątrz. Później wnętrze korpusu jest szlifowane ręcznie, ścięcia i krawędzie są sprawdzane i wygładzane, a nadmiar kleju usuwany. Jeden cal tolerancji zostaje zachowany na każdym krańcu korpusu celem późniejszego dokładnego ścięcia. Korpus jest następnie przycinany na prawidłową głębokość za pomocą laserowo prowadzonej maszyny. Podobnie, jak w przypadku Xiaoshan, ciężko doszukać się tu jakichś kopców trocin.
KROK 4 – ODPOWIEDNIE WYKOŃCZENIE
Rozpoczyna się długi proces wykańczania i trzeba tu naprawdę konkretnych fachowców. Technicy operują pistoletem natryskowym lepiej niż lakiernik w podwarszawskiej „dziupli” samochodowej w latach 90, szczególnie w przypadku efektu robienia cieni. Warstwy są nakładane stopniowo i ostrożnie. Oryginalne próbki są kontrolowane i porównywane podczas całego procesu, aby upewnić się co do poprawności wykończenia. Po pomalowaniu, korpusy pozostawia się na godzinę, aby podeschły w naturalny sposób, a następnie przenosi się je do ogrzewanego pomieszczenia o temperaturze 50° C. W zależności od wykończenia bęben może zostać w tym pomieszczeniu nawet przez pięć godzin.
KROK 5 – KRAWĘDZIE I WIERCENIE
Korpusy są umieszczane na specjalnie zaprojektowanej dla Yamahy maszynie. Krawędzie są mierzone przy pomocy lasera w czterech miejscach, następnie obliczany jest średni pomiar i krawędzie są cięte. Później są szlifowane i polerowane ręcznie. Prowadnice są umieszczane nad korpusem, aby skierować wiertło tam, gdzie powinny być wykonane otwory na lugi, otwór odpowietrzający itp. Wiertło nigdy nie przechodzi od razu całkowicie przez korpus, zatrzymuje się tuż przy powierzchni, aby uniknąć jakichkolwiek pęknięć.
KROK 6 – SKŁADANIE W CAŁOŚĆ
Podobnie, jak w fabryce w Xiaoshan, niebieskie skrzynki wypełnione są wszystkimi niezbędnymi komponentami, które trafiają na stanowisko montażowe wraz z gotowymi korpusami. Bębny są sprawdzane, „ubierane”, a naciągi zakładane z dużą starannością. Wreszcie ekskluzywna perkusja jest gotowa do wysyłki w świat!