Yamaha - zaglądając pod korpus. Jak to się robi?
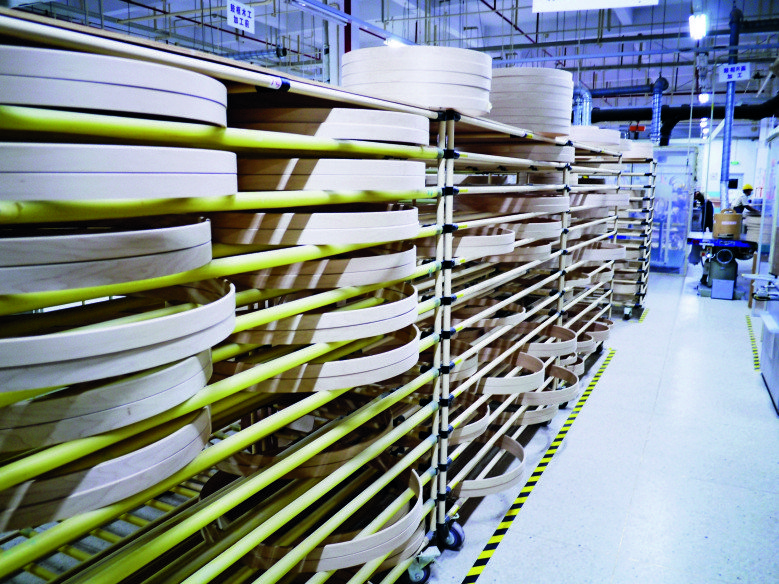
W poprzednich artykułach przedstawiliśmy historię firmy Yamaha, gdzie ukazaliśmy kolejne etapy rozwoju marki, muzyków, którzy grają na instrumentach firmy, a także zapytaliśmy Steve’a Gadda o zestaw Recording Custom. Rzuciliśmy też reporterskim okiem na japońską linię produkcyjną zestawów PHX.
Sęk w tym, ze PHX to koszt dość konkretny, ale na szczęście Yamaha ma w swojej ofercie zestawy z każdej półki, przeznaczone do każdego stylu gry. Właśnie, z jakim gatunkiem muzyki kojarzy się Yamaha? Bo niektóre marki bębnów niemal od razu są szufladkowane do danej stylistyki. Mamy tu jazzowego Steve’a Gadda, ale też thrashowego Paula Bostapha ze Slayer. Mamy hard rock u Tommy’ego Aldridge’a z Whitesnake i bębnienie fusion Dave’a Weckla. W Polsce progresywne pasaże robi Jurek Piotrowski, ale zaraz obok maluje w jazzowych klimatach Paweł Dobrowolski. Wszyscy spisują się doskonale i mają wspaniałe brzmienie.
Oprócz robionych na zamówienie PHX, katalog Yamaha obejmuje bębny klonowe (Tour), brzozowe (Recording oraz Stage Custom i Junior), dębowe (Live), mieszankę gatunków klonu i wenge (Absolute Hybrid), no i rzecz jasna topolę (Rydeen) dla tych, co jeszcze się zastanawiają, czy włazić w świat perkusji na całego.
Yamaha Stage Custom Bop kit
Yamaha Absolute Hybrid Maple
Yamaha Recording Custom
Jeszcze do niedawna za jakość produktów byli odpowiedzialni eksperci od Sakae, ale Yamaha dokonała zmian związanych z produkcją i jak przystało na korporację zoptymalizowała produkcję. Od razu pojawiły się wątpliwości co do jakości produktów, dlatego warto spojrzeć na ręce pracowników w Chinach.
To nie jest nasza pierwsza wizyta porównawcza fabryk japońskich i chińskich (robiliśmy to naocznie z Tamą, co można znaleźć na naszej stronie www.magazynperkusista.pl), więc wiemy, czego możemy się spodziewać. Dlatego z wielkim spokojem zapraszamy na przechadzkę.
NARODZINY BĘBNÓW YAMAHA
Wykonywanie wysokich modeli bębnów Yamaha to zaawansowany proces pod kątem logistycznym. Jak można się domyślić jest to nowocześnie ustawiona i zarządzana linia produkcyjna z kolejnymi stanowiskami odbioru i kontroli jakości. W fabryce Xiaoshan jest trzech managerów, odpowiadających za kolejne odcinki pracy: obróbka drewna, wykończenie i skład. Każdy z pracowników przeszedł szkolenie w głównej siedzibie firmy. Mieliśmy już niejednokrotnie styczność ze stylem pracy Japończyków, gdzie dbałość o szczegóły wydawać się może dla zwykłego Europejczyka wręcz męcząca… nawet dla Niemców, posługując się niegroźnymi stereotypami.
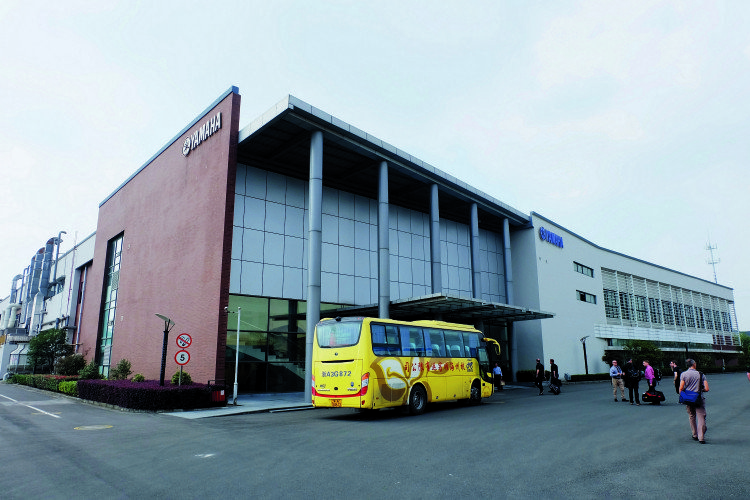
GDZIE: Podstawowa fabryka bębnów Yamaha – Xiaoshan, znajduje się w Hangzhou, we wschodnich Chinach. Hangzhou położone jest w odległości 4 godzin jazdy od Szanghaju.
KIEDY: Fabryka powstała w 1997 roku, by produkować części fortepianów, flety, klarnety, saksofony, trąbki, kornety, puzony i marszowe instrumenty perkusyjne. Nowa fabryka bębnów została zbudowana w 2010 roku, a cała produkcja bębnów została tam przeniesiona w październiku tego samego roku.
CO: Produkowane są tu najwyższej klasy serie Yamahy: Absolute Hybrid Maple, Live Custom i nowy Recording Custom.
DLACZEGO: Głównym celem była stabilność i niezależność produkcji, z tym wiążą się lepsze warunki pracy oraz opcje płynnego i szybkiego szkolenia pracowników. Istnieje możliwość rozbudowy obiektu w przyszłości.
LICZBY:
♦ 10 milionów dolarów zainwestowane w fabrykę bębnów.
♦ Fabryka posiada certyfikat ISO1400, co oznacza, że spełnia określone kryteria zarządzania środowiskowego.
♦ 560 pracowników, w tym 50 pracujących jedynie nad bębnami.
♦ Fabryka ma powierzchnię 31.500 metrów kwadratowych.
Xiaoshan to fabryka, gdzie znajdziemy specjalnie zaprojektowane dla firmy maszyny, ale wciąż interakcja między pracownikami jest najważniejszym elementem całego procesu. Czynnik ludzki ma największe znaczenie w momencie dokonywania inspekcji i kontrolowania jakości sprzętu. Może liczba 50 pracowników nie robi jakiegoś większego wrażenia, ale wiemy z doświadczenia, że przy współczesnym rozwoju technologii, znając dobrze proces tworzenia bębnów, jest to naprawdę duża liczba specjalistów.
Kolejna sprawa to sama fabryka i warunki w niej panujące. Wyobrażenie przeciętego Europejczyka o chińskiej fabryce nie idzie w parze nawet z najbardziej liberalnymi przepisami BHP. Tymczasem kolejny raz jesteśmy mile zaskoczeni. Duża czystość zapewniona przez wszelkiego rodzaju wywietrzniki i dmuchawy. Jest to nie tylko mniej szkodliwe dla samych pracowników, ale wpływa też na jakość budowanych bębnów. Nie ma tu ledwo żarzących się żarówek, tylko jasne światło, zapewniające komfort pracy i lepszą precyzję kolejnych czynności. Zbudowanie zestawu od podstaw zajmuje mnie więcej 12 dni, a wygląda to w skrócie tak:
KROK 1: SPRAWDZENIE ELEMENTÓW
Zanim przystąpimy do składania zestawu musimy dokładnie sprawdzić, czy dysponujemy odpowiednimi częściami i czy materiały, które mają wylądować na linii produkcyjnej, spełniają jakość. Nie ma mowy, żeby np. później młotkiem upychać na siłę jakieś elementy. Kolejne arkusze drewna są sprawdzane pod kątem różnych właściwości. Pracownicy patrzą, jak wygląda ich grubość, jakość faktury. Podobnie jest ze śrubkami, lugami, naciągami i innymi elementami, które wylądują na linii produkcyjnej. Wszystko jest notowane i w każdej chwili można zidentyfikować słaby punkt.
KROK 2: WYBÓR ODPOWIEDNICH CZĘŚCI
Bardzo ciekawa sytuacja już na samym początku, niespotykana na taką skalę w innych fabrykach. Pracownicy kompletują odpowiednie pakiety części w niebieskich pudełkach w zależności od tego, jaki model i rodzaj bębnów będzie tworzony. Po złożeniu korpusów pudełka zostaną odpowiednio dopasowane do zestawów.
KROK 3: SELEKCJA DREWNA
Arkusze drewna są składowane w oddzielnym pomieszczeniu. Później są dobierane i grupowane w zależności od rozmiarów i modelu bębnów. Każdy arkusz składa się z dwóch lub trzech warstw, co jest klasycznym sposobem tworzenia bębnów. Ułożone są słojami na przemian, horyzontalnie i wertykalnie celem wzmocnienia. Na tym etapie wszystkie arkusze są jeszcze bardzo elastyczne z racji wilgoci.
KROK 4: CIĘCIE
Teraz bierzemy się już faktycznie do roboty. Jak widać pomieszczenie jest utrzymane w dużej czystości. Arkusze brane są z wózków i cięte na konkretne rozmiary maszyną sterowaną komputerowo. W tym miejscu powstaje słynne diagonalne ścięcie Yamahy. Kąt ścięcia zależy oczywiście od rozmiaru bębna i modelu. Pracownik dostaje dokładną instrukcję na karcie działań.
KROK 5: KLEJENIE
Drewniane arkusze pokrywane są klejem, co wykonuje specjalna maszyna z wałkami, przypominająca wyżymaczkę. Co ciekawe, Yamaha stosuje tu specjalny klej, którego nie trzeba nakładać w dużej ilości, dzięki temu drewno nie dostaje dodatkowej dawki wilgoci.
KROK 6: FORMOWANIE KORPUSÓW
Sklejone warstwy są zwijane w odpowiednio dopasowanych formach, gdzie zaschną i się „złapią”. Lekko potraktowane „czujnikiem” (czyli pieszczotliwie mówiąc młotkiem) do odpowiedniej pozycji, by mieć pewność, że diagonalne ścięcie zetknie się idealnie z drugim końcem i powstanie uszczelnione połączenie. Równe łączenie rozłożone jest po całej szerokości, dzięki czemu korpusy mogą być cienkie, ale mocne.
KROK 7: ROZPYCHANIE I SUSZENIE
Kolejny ze znaków rozpoznawczych bębnów Yamaha. Zanim korpus zostanie wysuszony, do środka wkładana jest torba, która wypełniana jest powietrzem, przez co naciska na ścianki korpusu powodując, że bęben staje się okrąglejszy i bardziej zbity. Następnie korpus jest suszony w delikatnej temperaturze 50 stopni. Dzięki czemu bez większego szoku wilgoć powoli ginie i wysycha też klej. Większe formy do korpusów 22” i większych mają własne systemy nagrzewania.
KROK 8: SZLIFOWANIE
Zaczynamy żmudny proces wygładzania korpusów, dzięki czemu uzyskuje się nieskazitelnie gładkie korpusy, co ma kluczowy wpływ na dalszy etap nakładania wykończenia. Proces jest kilkukrotnie powtarzany. Korpus szlifowany jest wewnątrz i na zewnątrz przy wykorzystaniu różnych metod i układów. Maszyny dopasowują się automatycznie do wielkości korpusów.
KROK 9: USUWANIE RESZTEK KLEJU I DOCINANIE KORPUSU
Wnętrze korpusu jest sprawdzane i szlifowane ręcznie, żeby usunąć wszelkie ślady kleju ze szwów łączenia. Korpus jest docinany ostatecznie do odpowiedniego rozmiaru dzięki kolejnej maszynie sterowanej komputerowo z laserową dokładnością. Każdy korpus jest sprawdzany w czystym i dobrze oświetlonym miejscu.
KROK 10: POCZĄTEK WYKAŃCZANIA
Najpierw ogólnie – przechodzimy do nakładania kolejnych warstw lakieru, które przeplatane jest polerowaniem korpusu. Robione jest to zarówno maszynowo, jak i ręcznie. Lakier ma być nałożony równo, żeby korpus właściwie pracował. Bębny świecą się bardzo jasno, za co odpowiada system nakładania lakieru, jaki jest wykorzystywany przez firmę w pianinach i fortepianach. Każda firma ma swoją metodę. Mówiąc w skrócie jest około 20 kroków, związanych z wykończeniem bębnów, wszystko w zależności od bębna, drewna, z jakiego jest zrobiony i specyfiki farby. Dwa pierwsze z dziesięciu etapów polegają na wycieraniu i kolorowaniu, co daje bębnom bazową warstwę koloru do jakiego się dąży. Później korpus jest polerowany.
KROK 11: MALOWANIE
Korpus brany jest do nienagannie czystego boksu i malowany pierwszą warstwą. System kręcenia korpusu zapewnia równomierne rozłożenie warstwy. Korpusy są malowane ręcznie za pomocą pistoletów. Jak zawsze imponująco wygląda proces tworzenia cieni. Ściana wody za stanowiskiem gwarantuje pełne odpylenie podczas procesu malowania. Teraz kolejny raz bębny są polerowane.
KROK 12: WIĘCEJ FARBY, POLERKA I SUSZENIE
Dalej kolejna warstwa farby, polerowanie i górna warstwa farby. Po tym następuje… polerowanie oczywiście, aż wreszcie następuje miękkie polerowanie na błysk. Słynny system wykończenia UV robi się poprzez pozostawienie bębna na noc w temperaturze 50 stopni. Bębny, gdzie stosuje się system UV, są suszone tradycyjnie. Dalej mamy inspekcje koloru w oparciu o próbki. Nie ma możliwości idealnej powtarzalności przy ręcznej robocie, ale zakres tolerancji odchyłek od wzoru jest bardzo niski.
KROK 13: WYCINANIE KRAWĘDZI
Specjalnie zaprojektowana maszyna mierzy położony na niej korpus, przelicza i wycina odpowiedni rodzaj krawędzi korpusu. To samo dzieje się z łożem sprężyn w werblach. Krawędzie są szlifowane papierkiem o drobniutkim ziarenku i zabezpieczane.
KROK 14: WIERCENIE DZIUR
Każdy korpus ma swoją metryczkę, gdzie opisana jest cała specyfikacja wiercenia dziur, dzięki czemu po tak długim procesie tworzenia bębna nie ma możliwości pomyłki. Obręcze ze specjalnymi znacznikami dla każdego rodzaju bębna przymierzane są do korpusu, by mieć pewność, że dziury są nawiercane prawidłowo.
KROK 15: UBIERANIE
Teraz pojawiają się wreszcie wspomniane na początku niebieskie pudełeczka. Pudełka zawierają wszystkie niezbędne elementy, potrzebne do „ubrania” korpusu i stworzenia perkusyjnego bębna. Sprawne ręce pracowników doskonale wszystkim się zajmują. Na samym końcu mamy jeszcze jedną kontrolę i możemy powoli brać się za pakowanie bębnów, które ostatecznie trafią w ręce jakiegoś szczęściarza.
WNIOSKI
Trzeba przyznać, że Yamaha ma swoje metody budowania i wykańczania instrumentów. Zasadniczo cały proces tworzenia bębnów jest bardzo podobny w każdej fabryce. Do tej pory odwiedziliśmy linie produkcyjne DW Drums, Tama oraz Sonor. Etapy tworzenia są niemal identyczne w każdej z tych fabryk, a różnice dotyczą głównie rozwiązań technicznych, związanych z poszczególnymi procesami. Yamaha ma kilka własnych oryginalnych rozwiązań, co świadczy o tym, że firma wie, co robi. Czy są to rozwiązania, które czynią Yamahę najlepszym producentem bębnów na świecie? Bądźmy poważni i nie błaznujmy. Takiego określenia nie można zastosować w stosunku do żadnego z producentów bębnów na świecie. Za to można mówić tu o czołówce i z całą stanowczością Yamaha się w niej znajduje. Produkcja bębnów to jedno, druga sprawa to ludzie, którzy stoją za całym procesem prezentowania instrumentów innym ludziom. Nawet najcudowniejsza technologia nic nie wskóra, jeśli firma jest kiepsko reprezentowana. W przypadku Yamahy wszystko jest na szczęście jasne. Mamy materiały online i arcyciekawe katalogi drukowane, mamy polskie biuro i pracowników z krwi i kości, którym zawsze możemy pozawracać głowę.
Materiał przygotowany przez redakcje magazynu Perkusista, Rhythm i pomocy firmy Yamaha.