Produkcja talerzy Meinl Byzance
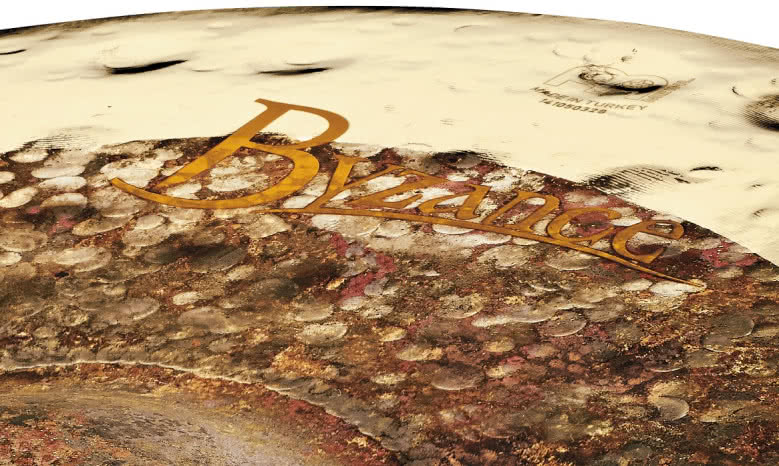
Prawdy i mity o rodzinie blach, która zmieniła świat talerzy perkusyjnych. Najwyższa możliwa półka jakościowa w katalogu talerzy Meinl.
Historię tej serii przedstawialiśmy kiedyś w skrócie na naszych łamach. Tym razem przyjrzymy się dokładniej jak wygląda proces produkcji, który wciąż rodzi wiele pytań i budzi kontrowersje ze względu na fakt, że są to blachy wykonane w Turcji.
Część turecka – etapy I i II, czyli piece, młotki, dłuta
Odbywa się w Turcji, w sposób tradycyjny dla tego regionu i obejmuje elementy, które są uzależnione od wymogów charakteru konkretnej serii. Mówiąc w telegraficznym skrócie, wygląda to mniej więcej tak jak poniżej.
Etap I - Przygotowanie talerza do obróbki:
-
przygotowanie odpowiednich proporcji brązu;
odlewanie brązu do odpowiednio dobranych form (w kształcie misek) w zależności od rodzaju przyszłej blachy;
czyszczenie odlewów/placków z popiołu;
rozgrzewanie placków w piecu;
wielokrotne rozgrzewanie i walcowanie do wymaganej grubości;
leżakowanie celem schłodzenia;
wycinanie centralnego otworu;
wycinanie okrągłej formy talerza;
podgrzanie talerza celem wybicia Bella;
hartowanie talerza (do tego momentu blacha jest bardzo krucha).
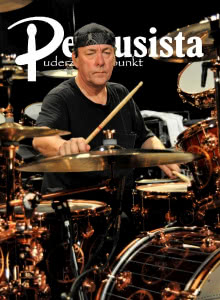